Dank 3D-Druckverfahren entwickelt die Forschungs- und Entwicklungsabteilung von KTM neue Motorräder und Komponenten noch schneller. Kann diese Technologie tatsächlich den Ansprüchen der rigorosen Tests und Standards bei Straßenmotorrädern des 21. Jahrhunderts genügen?
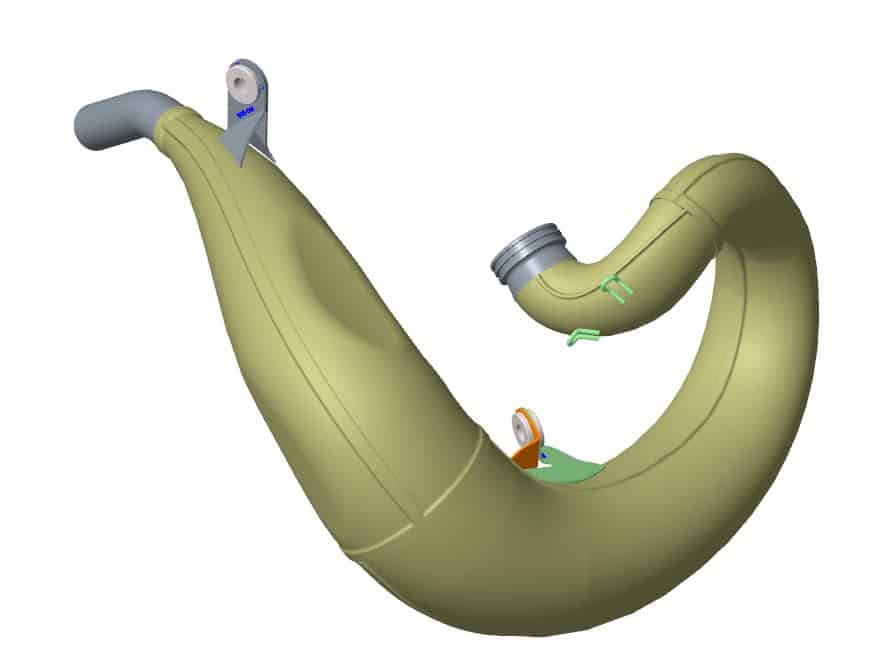
Es sieht danach aus, als wäre die Antwort ‚Ja‘. Im Frühsommer präsentierte KTM seine SX-Baureihe des Modelljahres 2019. Eine der wichtigsten Neuerungen bei der KTM 250 SX mit 2-Takt-Motor dreht sich um die Verwendung eines 3D-Druckers, um neue Ideen zur Weiterentwicklung der Auspuffbirne umzusetzen und diese zu testen.
Head of Engine Offroad & Motocross R&D, Michael Viertlmayr, erklärte, wie KTM die 2019er-Version entwarf, um das Gesamtpaket der Auspuffbirne zu verbessern und die Bodenfreiheit des Motorrads zu erhöhen. Neben 3D-Druckverfahren griff KTM dabei auch auf seine immer größer werdenden Erfahrungen in der MotoGPTM zurück und verwendete ovale Querschnitte, um seine Performance-Ziele zu erreichen. Natürlich ist die Theorie nur die eine Seite der Medaille. Die andere ist, die Komponenten an einem echten Bike zu testen.
„Wir haben einen Innovationszyklus“, so Viertlmayr. „Dieser beginnt mit einem Grundkonzept oder mit der Idee, die Auspuffbirne zu verkleinern oder schlanker zu machen. Wir wussten um die Vorteile ovaler Querschnitte und wollten die Auspuffbirne näher am Rahmen verlegen. Mit Hilfe des 3D-Modells beginnen wir dann eine Simulations- und Berechnungsphase. Wir gehören zu den wenigen Unternehmen auf der Welt, die in der Lage sind, die hochkomplexe Thermodynamik eines 2-Takt-Motors zu berechnen, was viel schwieriger ist als bei einem 4-Takter.“
„Sind wir mit den Ergebnissen der Berechnungsphase zufrieden, bauen wir den ersten Prototyp“, fährt er fort. „Wenn wir mit den Ergebnissen nicht zufrieden sind, startet eine neue Schleife mit der Design-Abteilung. Wenn die Berechnungen vielversprechend sind, drucken wir die Segmente aus, schweißen sie zusammen und schon haben wir einen voll funktionstüchtigen READY TO RACE-Auspuffbirnen-Prototyp.“
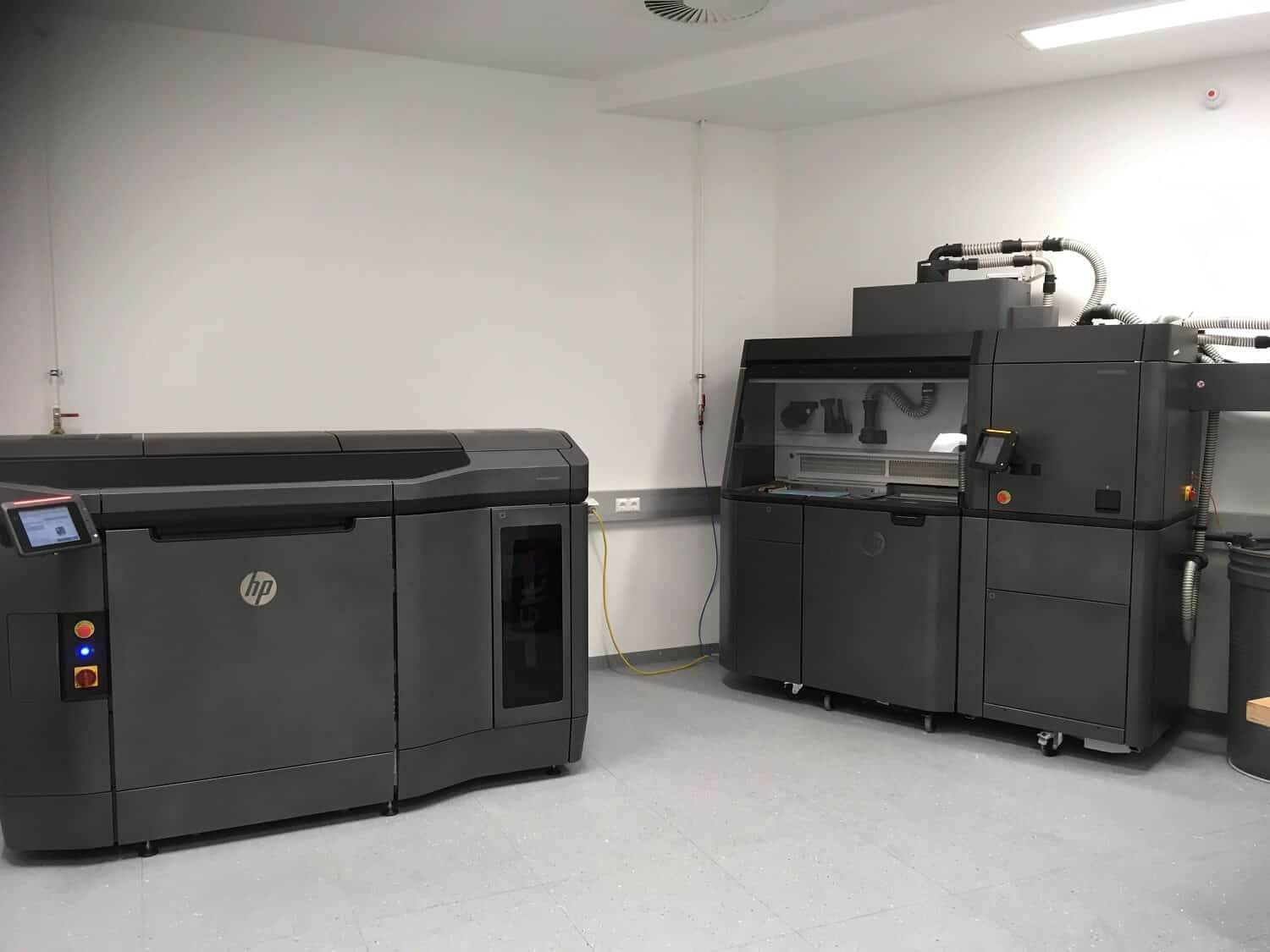
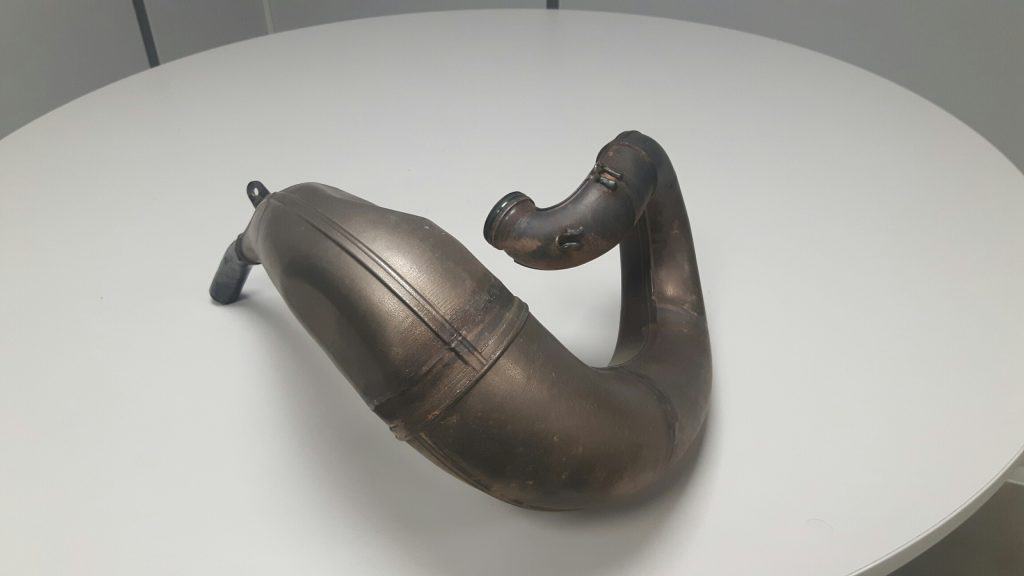
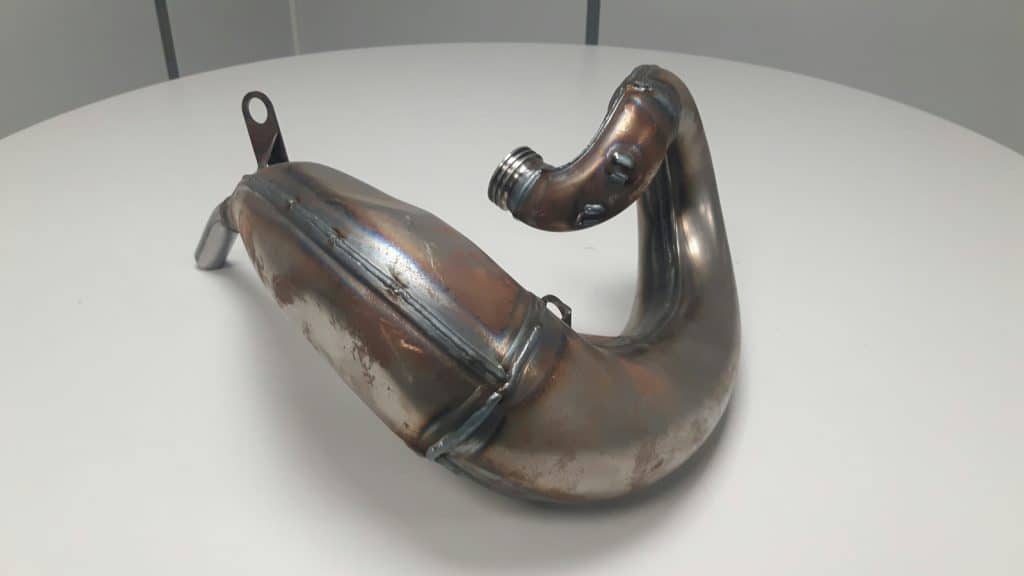
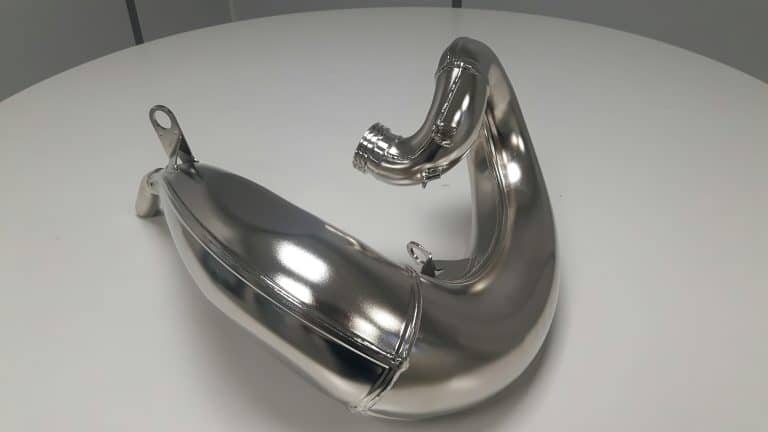
„Wir haben die Möglichkeit, neue Teile am Prüfstand und von unseren Testfahrern auf der Strecke testen zu lassen. Das liefert jede Menge Feedback und Zahlen. Sind wir mit dem Design zufrieden, folgt die zweite Prototyp-Phase.“
Die Vorteile liegen auf der Hand. „Wir sparen damit extrem viel Entwicklungszeit“, so Viertlmayr. „Die Segmente eines Auspuff-Prototyps zu drucken, dauert weniger als eine Woche, was uns alleine 2-3 Monate spart. Das macht uns das Leben deutlich leichter. Die gedruckten Teile sind voll funktionstüchtig. Es handelt sich nicht um Entwurfsteile; sie können am Prüfstand und auf der Strecke getestet werden, was einfach fantastisch ist und einen großen Schritt vorwärts darstellt.“